Green on the Go
Metals: Fuel of the Future
The maritime shipping industry is an area of great importance. In a world where goods from all over the world can be shipped to your doorstep with just a few clicks, ocean-faring ships are the backbone of worldwide trade. However, they have a great impact on our climate. In 2018, the global shipping industry was responsible for 1056 million tonnes of carbon dioxide emission—2.89% of total global emissions—and these numbers are projected to rise. That’s why many different alternatives are being developed. Recently, a new carrier of energy started to gain attention: metals. In 2019, Eindhoven University of Technology and the Maritiem Kenniscentrum researched the feasibility of metal-powered ships. They concluded that it’s feasible, but there are some hurdles ahead.
In a usual burning process, fuels like diesel or heavy fuel oil are burned and react with the oxygen in the air. This reaction releases a lot of energy—burning diesel, for example, releases about 45.5 MJ per kilogram—but it also forms the dreaded carbon dioxide. A similar reaction takes place if a metal is burned. The metal powder reacts with the oxygen in the air and releases energy, but instead of carbon dioxide, metal oxides are formed. After the burning process, these metal oxides can be recovered from the boiler or be caught by filter systems. The metal oxides then can go through a process of reduction, wherein energy is put in to remove the oxygen from the compound and the original metal is returned, making metals a renewable energy carrier.
This process works for various different metals, like iron and aluminium. However, according to Dr Roy Hermanns, a researcher connected to the research on the combustion of metals at Eindhoven University of Technology, it takes a very high temperature to make many of these metals react with oxygen. For example, aluminium has to reach 3268°C before it reacts—a temperature much higher than the reaction with a fuel like diesel (≈2000°C). Implementation of metals like these would lead to whole new system requirements.
One of the exceptions to this is iron. For iron, the temperature needs to be only 1955°C for the reaction with oxygen to take place, meaning the system requirements will remain largely similar. Iron also has other benefits, like its abundance on planet earth. In addition to the possibility of regeneration, this makes iron a long-term stable fuel source. Also, due to existing research in the steel industry, it is possible to reduce iron oxides w
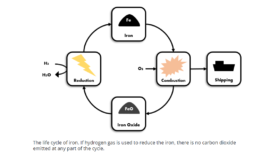
ith the help of hydrogen gas. Through this method, which is already in use in the Circored process, the oxygen reacts with the hydrogen gas and forms water. If the hydrogen gas is produced with renewable energy, the entire cycle is completely carbon dioxide free.
The technology of burning iron for energy has a broad range of applications. Several companies and groups have tested it for industrial processes, like student team SOLID of Eindhoven University of Technology. In 2019, their 100 kW Metal Power system was put into practice at Royal Swinkels Family Brewers, where it successfully produced enough steam to power the brewing process of the beer. Team SOLID was also involved in the report on the technical and economic feasibility of the process for maritime purposes. In conjunction with the Maritiem Kenniscentrum and several scientists of the TU/e, case studies were made for ships of three different sizes: the small research vessel Pelagia, the mid-size containership Rijnborg, and the large containership Emma Maersk. The report concluded that the use of iron as an energy carrier to power ships is feasible in the future and that the technology can be added to the list of alternatives being developed.
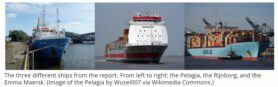
However, according to the report, one has to keep in mind several things, like the weight of iron. The amount of energy you get from burning a kilogram of iron is 7.4 MJ—a lot less than burning a fuel like diesel. If a mid-size vessel like the Rijnborg wants to keep the same action radius as it does with its current fuel, the ship would have to be 35% to 50% longer to create more carrying capacity. The technology also is more economically interesting for larger size vessels. The report concludes that—scaled to their sizes—the cost of implementation on the Emma Maersk is 40% less than the cost on the Rijnborg. However, the cost to operate the technology is within reasonable boundaries for both ship sizes, as it’s possible to break even by shipping containers within the ships’ capacities.
The report also lists the future of research that has to be done before this becomes a reality. For example, the efficiency of the boiler needs to be increased, the iron oxides need to be caught more efficiently, and further research into the initial and operational costs has to be done. Hermanns adds that we need to make steps in policy making too. Because large container ships are faring across international borders, policies have to change globally. For example, many countries have set norms for what constitutes as a fuel. Iron has to be added to that list.
Although it has not yet actually been tested on board of a ship, it is likely that iron will be an interesting option as an energy carrier. However, it won’t be the solution for all of our ships. According to Hermanns: “There is not just one technology that will end up being used [exclusively]. For every application, you have to research what is the most energy and cost efficient.” For shorter travels and smaller ships, hydrogen, batteries, or other solutions might end up being better options. However, there is a probability that, in the next decade, your package from across the globe will be shipped to you on a containership powered by iron.